A Canadian company that uses industrial robots, AI and the latest technology to produce housing offsite is expanding its production lines at a sprawling facility in an industrial park in Calgary.
Promise Robotics plans to produce one million square feet of housing annually by turning off-the-shelf robots into autonomous production systems that can build homes faster with less resources.
Historically, adopting automation in construction required massive capital and specialized expertise but the company hopes to change that with its Homebuilding Factory-as-a-Service platform.
“Our AI transforms decades of homebuilding knowledge into software that enables off-the-shelf robots to perform skilled construction tasks,” says company co-founder and CEO Ramtin Attar.
“This is the leap the industry needs – from CAD-CAM machines to intelligent, adaptive systems that understand how to build.”
Traditional automation in manufacturing assumes repeatability, but construction doesn’t offer that luxury as every home is different. The company uses “thinking” machines to get around that.
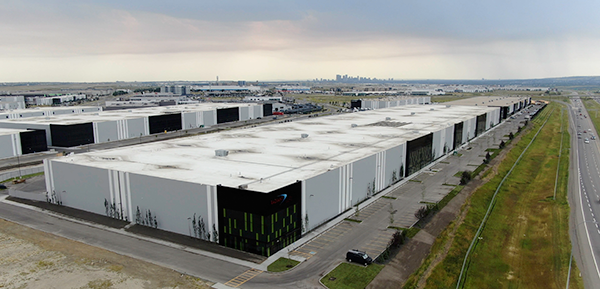
“A single wall may require over 200 distinct actions involving tools, material handling and skilled decision-making,” says Attar. “Our AI model serves as a digital tradesperson, continuously learning construction logic and executing tasks that were previously possible only by experienced human hands.”
Specialized software converts architectural plans into manufacturable components. Then, an AI brain generates step-by-step robotic instructions optimized for efficiency and speed.
“Speed isn’t just about fast robots – it’s about shortening the entire path from design to site assembly,” says Attar. “Our platform integrates production and logistics into a seamless, end-to-end system that enables faster and smarter home construction.”
The platform eliminates complex processes and can produce homes for onsite assembly in half the time of a conventional home.
The facility will be the company’s second in Canada. It presently has one in Edmonton. The plan is to expand to cities like Houston, Dallas, Phoenix, Atlanta, Charlotte, Austin and Nashville.
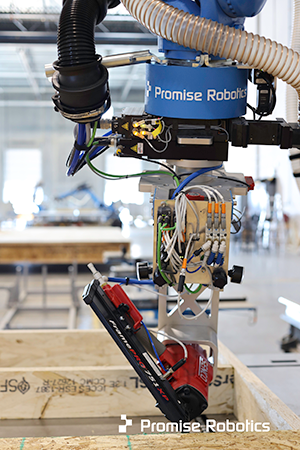
The Calgary facility is being built in a 60,000-square-foot warehouse north of Calgary Airport off Deerfoot Trail NE. The site was chosen because of Calgary’s rapid growth and commitment to innovation.
“This facility not only supports regional builders but will also demonstrate our state-of-the-art AI-driven production lines in action to international markets,” says Attar.
The facility will have a cloud-based industrial AI system that will demonstrate the full spectrum from preproduction planning to estimating, logistics and installation. The facility will feature intelligent, task-adaptive robots that can change tools and workflows based on production needs.
Attar says the machines can be set up in weeks and ready to go.
“The most time-consuming part is waiting for the building and occupancy permit. We’re on track to begin production in August.”
The AI brain can scan building plans and make decisions about the fastest way to build. Robots will be able to read blueprints and decide for themselves what cuts to make, what pieces to nail together and where holes need to be drilled for wires and plumbing.
With a single purchase order, the factory will be able to produce a complete structure with walls, floors, stairs, roofs, windows, doors, waterproofing, and mechanical, electrical and plumbing penetrations.
The factory will be able to produce single-family to multi-unit dwellings as well as customized projects.
“We don’t require standard designs. Our foundational AI knowledge system is flexible enough to produce any wood-framed structure that production builders currently construct in Canada or the U.S.,” says Attar.
He notes homebuilders will benefit from the speed, safety and efficiency of the operations.
“Builders benefit from simplified procurement, faster production, predictable budgets and schedules, reduced rework and warranty claims, and scalable capacity without increasing overhead.
“Our process enhances job site safety, quality, and sustainability while accelerating project timelines.”
Attar says the platform was built in Canada by builders for builders and empowers construction companies nationwide to construct more homes faster.
“We are redefining the future of prefabrication and making it a scalable nationwide solution with Canadian-born AI.”
In light of the housing supply and affordability crisis Canada is facing, Attar says the platform will enable developers to speed up the building process. However, it is not a silver bullet.
“Canada’s housing crisis is also a productivity crisis,” he states, and “the homebuilding sector faces an aging workforce, labour shortages and low digitization rates. Even if we removed every regulatory hurdle, the industry lacks the scalable capacity to build at the pace needed.”
Attar notes the construction sector has been slow to innovate, mainly due to the fact the industry is fragmented and comprised of many small businesses that are not equipped financially or knowledge-wise to invest in innovation, but Promise Robotics is embracing the opportunity.
“While industries like automotive have improved productivity and reduced costs, construction costs have risen while efficiency has declined. We need updated regulatory and financing models to support innovation – and industry leaders willing to drive systemic change.”
While the threat of tariffs being imposed by the Donald Trump administration has shaken the construction industry and cross-border operations, Attar says Promise Robotics intends to get around that thorny problem by deploying its production systems regionally to serve local markets.
“This distributed model avoids the need to move physical products across borders,” he says, “insulating us and our partners from cross-border tariffs or trade uncertainties.”
Recent Comments